Customization Options
Compact Aerospace Lathe
Precision Lathe Inside Chamber
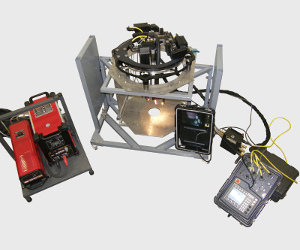
Portable XM System for In-field Cladding
Custom Coordinated Motion System
One of AMET’s greatest strengths is the ability to customize systems to meet the needs of our customers. Whether your needs are for a completely custom system or adding a single component to one of our more standard products, we can accommodate your needs and build a first-class automated welding system.
AMET’s whole-system approach and our control architecture allow us the ability to modify and create software and hardware to satisfy most needs. In 25+ years we have developed features, functions, hardware, and software specifically designed to meet the demands of a large customer base, so if you don’t see the feature or function you need listed below, contact us to discuss. Odds are, we have previously created and integrated the same function or something similar. If not, we can most likely develop the necessary solution.
We offer the following Options:
Seam Tracking and Camera Systems
SAW Laser Seam Tracker and Camera
- Laser Seam Tracking – A laser scans the joint profile and allows the operator to select a point for the system to track. The laser continuously scans the joint throughout the weld and automatically adjusts to any variations in the part to ensure the torch remains in the programmed location. Laser systems are configurable for single and multiple pass welds and most processes.
- Camera Systems
- Arc Viewing Solutions for GTAW and PAW applications. AMET tailors each camera system to meet the requirements of each project. Cameras can be purchased individually, as a package with a monitor, or as an integrated component of a system.
- Video solutions with laser cross-hair generator for SAW applications. The camera packages are very beneficial in initial setup and positioning of the weld head, especially from remote locations. They also aid in monitoring the welding process.
- Arc Viewing Solutions for GTAW and PAW applications. AMET tailors each camera system to meet the requirements of each project. Cameras can be purchased individually, as a package with a monitor, or as an integrated component of a system.
Arc Viewing Camera Monitor
Motion Control

Mechanical Oscillation Video
- Oscillation Control – There are two types of oscillation available
- Magnetic Oscillation – Magnetic probe is used to deflect the arc back and forth for excellent sidewall tie in. The arc can also be deflected and maintained in a set position. This can be beneficial for fillet or otherwise hard-to-reach joints.
- Mechanical Oscillation – A precision servo motor driven ball screw slide provides mechanical oscillation. The oscillation motion is completely programmable including dwell time, frequency, width, and travel speed.
- Magnetic Oscillation – Magnetic probe is used to deflect the arc back and forth for excellent sidewall tie in. The arc can also be deflected and maintained in a set position. This can be beneficial for fillet or otherwise hard-to-reach joints.
- AVC (Arc Voltage Control) – A precision servo motor driven ball screw slide provides automatic adjustments to maintain a constant arc voltage standoff.
- Touch Start – Arc initiated by touching the torch tip to the part for GTAW and PAW applications.
- Coordinated Motion Module – Up to four motion axes can be integrated together. This allows each axis to function and coordinate together much like a CNC milling machine to perform welds on unique part geometries.
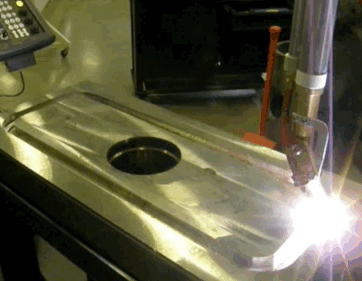
Coordinated Motion - Video Speed is 8x
Weld Automation, Gas Control, PLC Control, and Sensors

Automatic Part Loader
Double Touch Joint Locator
- Weld Automation Capability – Ability to program up to 10 pre-weld and 10 post-weld tasks into the weld schedule. These tasks include motion to defined positions, move to home, start or stop delays, gas on/off, and integration with external equipment such as:
- Part Loaders – Automatically loads the next part into the system upon completion of previous part.
- Part Clamping – Pneumatically of hydraulically controlled part clamping devices are activated once the part is in position.
- Joint Locator – Uses torch to touch the part in two places to locate the joint.
- Part Loaders – Automatically loads the next part into the system upon completion of previous part.
- PLC Controls – Continuously monitor aspects of the system to ensure tasks are performed.
- Safety Measures – Certain criteria must be met prior to welding or during the weld to prevent damaging the system or harming the operator.
- Automated Weld Screens – Protect operator from arc.
- Laser Light Curtains – Prevent injury to the operator during welding. If the laser beam is broken during welds, the program stops.
- Automated Weld Screens – Protect operator from arc.
- Safety Measures – Certain criteria must be met prior to welding or during the weld to prevent damaging the system or harming the operator.
- Programmable Gas Control – Flow rates are programmable for GTAW and PAW applications.
- Gas Sensors – Monitors shield/backing gas levels and automatically terminates the weld program if levels are too low.
- Humidity Monitoring Sensors – Monitors humidity levels and automatically terminates the weld program if levels are too high.
- Oxygen Monitoring Sensors – Monitors oxygen levels and automatically terminates the weld program if levels exceed set values.
- Water Sensors – Monitors water flow levels for torch and other cooled components and automatically terminates the weld program if levels are too low.

Automated Part Clamping
Weld Heads
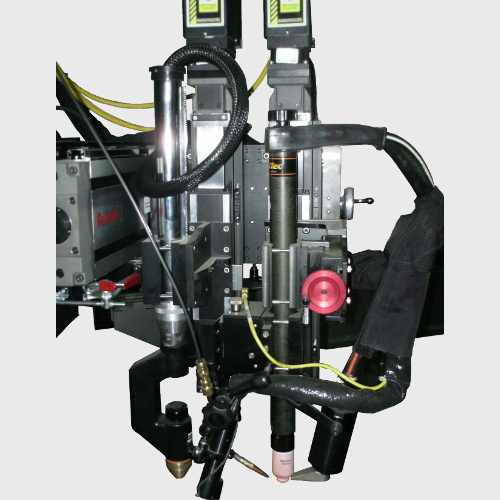
TIG & Plasma Weld Head
AMET designs and develops weld heads that are specific to each weld process and application. We produce weld heads with a wide range of capabilities and features from single process to complex. Below are some of the weld heads AMET produces.
- Multi-process – Multiple processes are integrated into a single weld head to maximize productivity and increase part welding capabilities. AMET produces TIG and Plasma, Subarc and MIG, and TIG Plasma and MIG weld heads.
- Multi-wire – Multiple wires are incorporated into a weld head, which increases wire deposition rates. We produce weld heads with up to 10 wire configurations.
- Continuous Rotation – Continuous rotation for operations such as cladding without the need for rotating equipment such as turn tables or positioners. The weld head includes a slip ring so all connections, including camera cables, can pass through without becoming entangled or losing connectivity.
- Internal Welding – AMET produces several variations for internal welding applications. These weld heads often require significant design efforts to ensure they will fit inside a confined opening for ID welding. They include multi-process or multi-wire configurations.
- Narrow Gap – AMET offers tandem wire narrow gap weld heads for SAW applications. The narrow gap is designed to weld in tight joint profiles that would be not be feasible using a standard SAW configuration. The weld head features tandem wire and each weld tip includes motorized motion for independent operation, which improves sidewall tie in capabilities. AMET is currently developing a single wire Narrow Gap GTAW weld head. Please contact us for additional information.
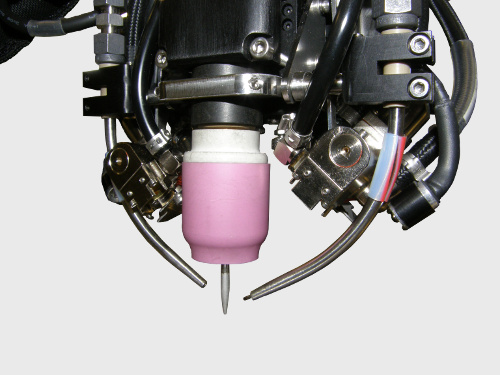
Dual Camera Weld Head
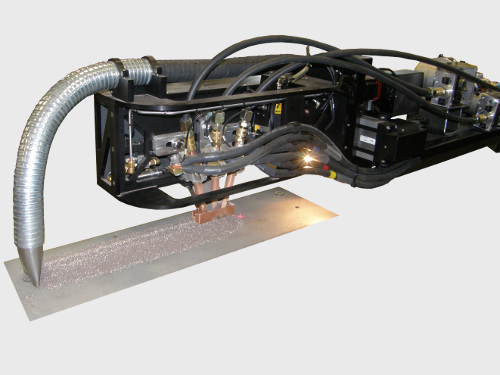
3-Wire ID SAW Weld Head
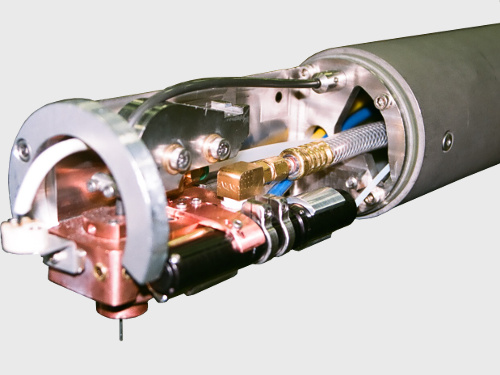
ID GTAW Weld Head
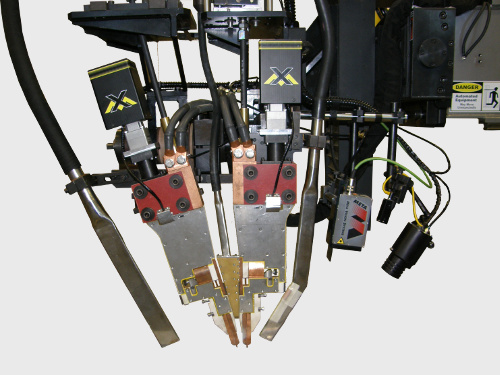
SAW Tandem Wire Narrow Gap
Software Options
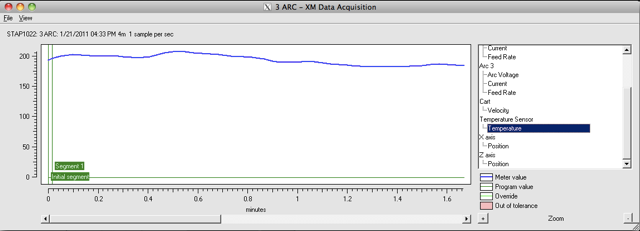
Data Acquisition and Tolerance Checking Software
Clad Intersecting Bores
- Data Acquisition and Tolerance Checking – Real time monitoring of the actual weld parameter values compares them to an operator defined tolerance range. If the values are outside of the tolerance range then the operator can either be alerted or the program can be terminated automatically. Collected data may be viewed on controller screen or exported as a .csv file for graphing and review with a program such as Microsoft Excel.
- Bar Code Program Selection – Bar code scanner is integrated with AMET controls to automatically select and load the corresponding weld program for each part. This helps eliminate loading the incorrect program when a large range of parts are welded or when weld programs are changed frequently.
- Offline Programming and Storage Capability – Weld programs can be created, modified, or stored on a PC. These programs can be moved back and forth between the controller and the PC using a USB storage device or through an Ethernet connection.
- Virtual Alignment Capability (Teach Mode) – Ability to define a linear or circumferential path with two or more defined or “taught” points. Once a path is defined, the system will retrace each defined point to create a custom weld path. The defined path can also be used for multiple pass welds or as an offset subsequent passes.
- Automation Software Capability – Allows the ability to program up to 10 pre-weld and 10 post-weld programmable tasks. These tasks include motion to defined positions, move to home, start or stop delays, enable or disable any integrated external component, gas on/off, and safety interlocks.
- Cladding Options – The following cladding applications are available
- Spiral Path Control – The vertical or horizontal axis is integrated with the rotary axis to provide precise cladding motion. Welds begin at the bottom of the part and spiral upward until the defined height is reached. The pitch of the spiral is programmable.
- Step-Index Control – The vertical or horizontal axis is integrated with the rotary axis to provide precise cladding motion. After each revolution is completed, the torch steps upward and begins the next pass. This is repeated until the defined height is reached. Step height is programmable.
- Intersecting Bore Cladding – Automatically clads around intersecting bores that are on center and perpendicular to tangent.
- Complex Intersecting Bores – Automatically clads around intersecting bores that are off-center and off-angle.
- Spiral Path Control – The vertical or horizontal axis is integrated with the rotary axis to provide precise cladding motion. Welds begin at the bottom of the part and spiral upward until the defined height is reached. The pitch of the spiral is programmable.
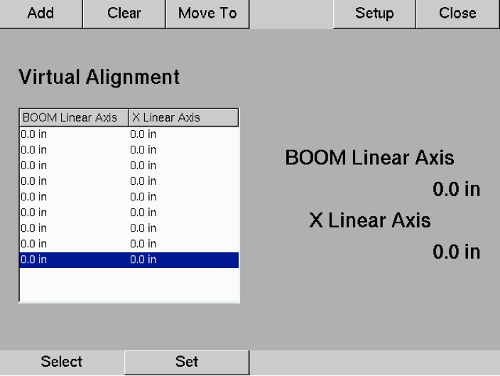
Virtual Alignment Software