Standard Features on Integrated Pipe Spool Welding Station
1
The SX Controller is the center of this turnkey welding system. The SX uses digital controls for integration with the welding power supply, hotwire feeder, AVC, and oscillator. The user interface offers an intuitive and logical layout to quickly and easily create, edit, and store weld programs.
2
The Roll Out system features several manual torch adjustments, which creates a versatile system. The torch has +/- 20 degrees of lead and lag (Y-Axis) adjustment, +/- 45 degrees of tilting (X-Axis) capability, and 5.5 in (140 mm) over-center adjustment to facilitate a large range of part diameters and joint configurations.
3
Two (2) precision ball screw slides driven by a servo motor with encoder feedback are included for programmable motion of the torch in the X-axis and Z-axis. The X-axis includes mechanical oscillation capability and the Z-axis is equipped with AVC. Both axes are programmable and include velocity and position control to ensure consistent and repeatable performance.
4
A 4-roll wire drive assembly that is driven by a servo motor with encoder feedback provides precision wire delivery. Wire feed speed, start delay, and wire retract are each programmable with the SX Controller. The wire feeder offers high-precision wire delivery with an accuracy of +/- 1% of the programmed speed. The wire feeder also includes a manual hotwire nozzle positioner that is mounted to the torch.
5
The manipulator features robust construction with thick-wall steel tubing for a long service life. The manipulator has a fixed-boom with motorized height adjustment. The height adjustment is used for positioning of the weld head only, so it will not be integrated into the SX Controller. However, precision rails and bearings are included to ensure longevity and smooth operation.
6
A GTAW sensor box is included to provide integration of the gas and water sensors. A digital solenoid and manual flow meter are incorporated for programmable on/off control of the shield gas. A gas sensor is included to detect the presence of gas and a water sensor for the presence of water flow from the circulator. If no gas or water is sensed, the SX will receive an error. These sensors help protect vital components and maintain weld integrity. Additional gas control can be added for backing or trailing gases.
7
An electrical control cabinet is included to provide a central location for all control modules and electrical components. Included in this package is a single point power distribution that provides fuse-protected power to the entire system from a single primary power circuit (provided by client).
8
The manual travel cart provides secure housing for the welding equipment (power supply, hotwire power supply, and water circulator), manipulator, and electrical control components. The travel cart can easily be pushed or pulled to the desired position along the length of the 20 ft (6096 mm) rails and then locked into place with a manual brake.
9
The AMET Hotwire power supply provides a true high precision RMS output of up to 200 amps at up to 20 volt AC. This reduces arc deflection (arc-blow) commonly found in DC hot wire units.
10
One (1) pipe support stand is included with the system to provide part support opposite the headstock. The idler wheels are capable of safely supporting pipes from 2 to 48 in (50.8 to 1219 mm) OD. The stand height is manually adjustable from 24” – 36” (609 to 914 mm).
11
Precision and programmable rotation is performed by the headstock. A servo motor with encoder feedback drives the headstock for precise control of the pipe rotation. The headstock includes a three-jaw gripper for holding/clamping parts.
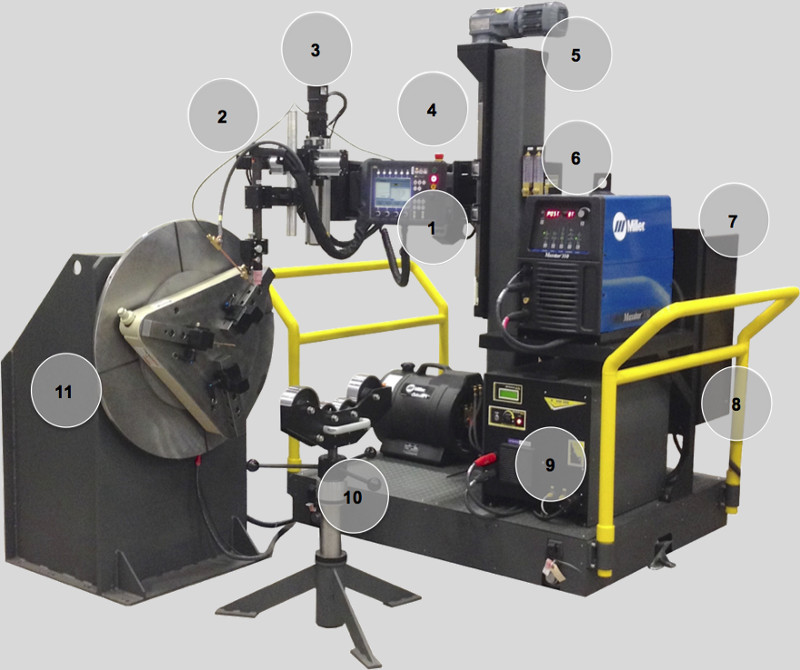