Standard Features on Column and Boom Manipulator Systems (Heavy Duty)
1
1) A weld head is attached to the end of the boom, which typically includes two precision motorized slides for moving the torch vertically and horizontally. Torch tilting, pivoting, and lead/lag adjustments are available to accommodate most types of weld joints.
2
2) The motorized boom features thick wall steel construction that is stress-relieved to extend the life and increase the precision of the manipulator. The boom is equipped with a variable speed motor for in/out horizontal motion.
3
Vertical boom motion is provided by a fixed speed motor with a brake to prevent unwanted movement. The manipulator features a heavy-duty chain drive to move the boom up/down and an anti-fall safety device to prevent the boom crashing to the factory floor should the chain lift fail.
4
Cable carriers are included on both axes to extend the life of the cables and hoses. The carriers also keep the cables organized and prevent entanglement during operation.
5
THK style rails are included for the entire length of the column and boom motions. The rails coupled with recirculating bearing blocks ensure smooth operation throughout the life of the manipulator.
6
The column features a kingpin for 360 degrees of manual rotation with four manual brakes to lock the column into postion. A handle is included on larger manipulators to aid in rotation.
7
A sturdy freestanding base supports the manipulator fixture. Each leg of the base includes a hole that can be used for anchoring the manipulator to the factory floor for additional stability.
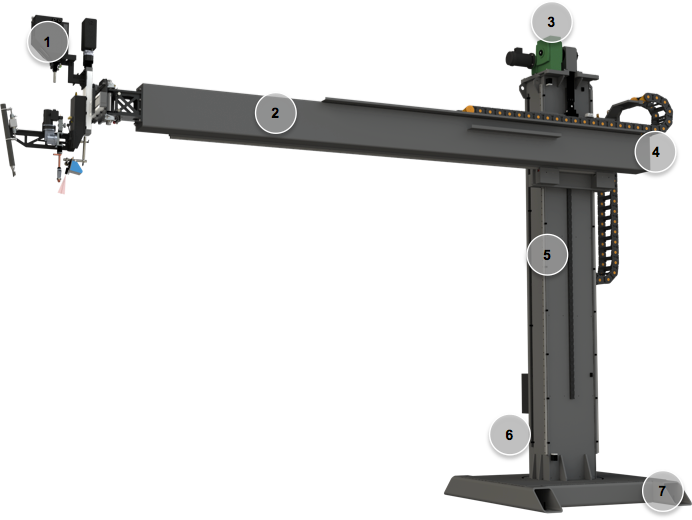