Standard Features on Precision Benchtop Linear Seam Welder
1
A travel carriage rides on four (4) precision linear rail bearing blocks and is driven by a ballscrew drive system. The ballscrew is directly coupled to the servo motor and, through closed loop encoder feedback, provides extremely high levels of precise repeatable movements. Home and travel limit switches are included, further enabling precise and repeatable welds. A cable tray and cable carrier provides a neat cabling package, as well as extending the life of the cabling and hoses running to the seam welder carriage and weld head.
2
The seam welder track is stress relieved prior to machining, which maintains tight tolerances and dimensional stability over the lifetime of the equipment. The track is outfitted with precision ground linear rails which provide smooth, repeatable motion resulting in superb welds.
3
Two (2) manually retractable part alignment devices facilitate positioning of the weld joint along the centerline of the seam welder prior to clamping and welding. These alignment devices may be easily repositioned along the length of the seam welder bed, allowing them to be placed appropriately for parts of varying lengths.
4
A safety interlock switch is provided at the mandrel latch. The integration of this switch prevents the seam welder from clamping when the mandrel latch is in an open condition. It also prevents unclamping while the weld is in progress.
5
Double wall pneumatic hose provides uniform clamping force to each of the seam welder clamping fingers along the full length of the weld. A pressure regulator is provided to allow adjustment of the clamping force. The aluminum clamping fingers are fitted with copper fingertips that are reversible to double their service life. The copper fingertips provide excellent heat conduction and aid in chilling the weld zone during the weld. The seam welder’s fingertips may be replaced individually as needed.
6
The finger-to-finger distance between the front and back clamping fingers may be adjusted, thus allowing the fixture to be fine-tuned to the welding process and materials being welded. The range of adjustment allows finger-to-finger distances of 0.1 to 0.8 in (3 to 20mm).
7
The adjustable height seam welder mandrel accommodates materials of various thicknesses. The mandrel is supplied with one (1) standard copper insert. The groove in the insert is machined to match the material type and thickness that is being welded, as specified by the client.
8
AMET Seam Welders utilize heavy duty, thick wall structural steel construction to minimize part distortion during clamping. The added mass also provides superior heat absorption and dissipation during the welding process, while at the same time increasing the rigidity and extending the equipment’s service life.
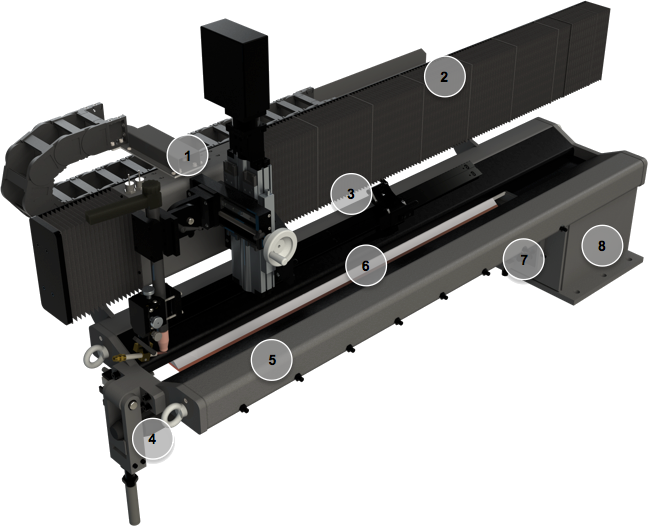